In today’s rapidly evolving technological landscape, integrating specialized hardware solutions can significantly enhance automation, data acquisition, and simulation capabilities. Whether for industrial applications, hobbyist projects, or research, tools like the PoKeys57E, RC simulator interfaces, Raspberry Pi temperature loggers, and DAQ devices play pivotal roles in streamlining processes and improving efficiency.
This article explores these four key technologies, their functionalities, and how they can be applied in real-world scenarios. The PoKeys57E serves as the central focus, given its versatility in automation and control. We will also examine how RC simulator interfaces enhance remote-controlled vehicle testing, how Raspberry Pi temperature loggers provide cost-effective environmental monitoring, and how DAQ devices ensure precise data collection in industrial settings.
PoKeys57E – The Ultimate Automation and Control Interface
The PoKeys57E is a powerful, multifunctional USB device designed for automation, robotics, and custom control applications. Combining digital and analog I/O, encoder inputs, PWM outputs, and even keyboard emulation, the PoKeys57E serves as a versatile hub for both industrial and hobbyist projects. Whether you’re building a custom CNC controller, a home automation system, or a flight simulator cockpit, the PoKeys57E provides the flexibility and precision needed for seamless integration.
Key Features of the PoKeys57E
One of the standout aspects of the PoKeys57E is its extensive I/O capabilities. With 57 configurable pins, it supports digital inputs and outputs, analog inputs, PWM signal generation, and encoder interfaces. This makes it ideal for tasks such as reading sensor data, controlling motors, or interfacing with custom switches and buttons. Additionally, the PoKeys57E includes a built-in keyboard emulator, allowing it to send keystrokes to a PC—perfect for simulator setups where physical inputs must trigger software responses.
Another major advantage is its plugin-free operation. Unlike many control interfaces that require proprietary drivers, the PoKeys57E is recognized as a standard HID (Human Interface Device) by most operating systems. This plug-and-play functionality ensures quick setup and broad compatibility with Windows, Linux, and even Raspberry Pi systems.
Applications in Automation and Simulation
The PoKeys57E excels in automation projects where multiple input and output signals must be managed efficiently. For example, in a custom home automation system, it can read signals from motion sensors, control relays for lighting, and log data via serial communication. Similarly, in industrial settings, the PoKeys57E can interface with PLCs (Programmable Logic Controllers) to provide additional I/O expansion where needed.
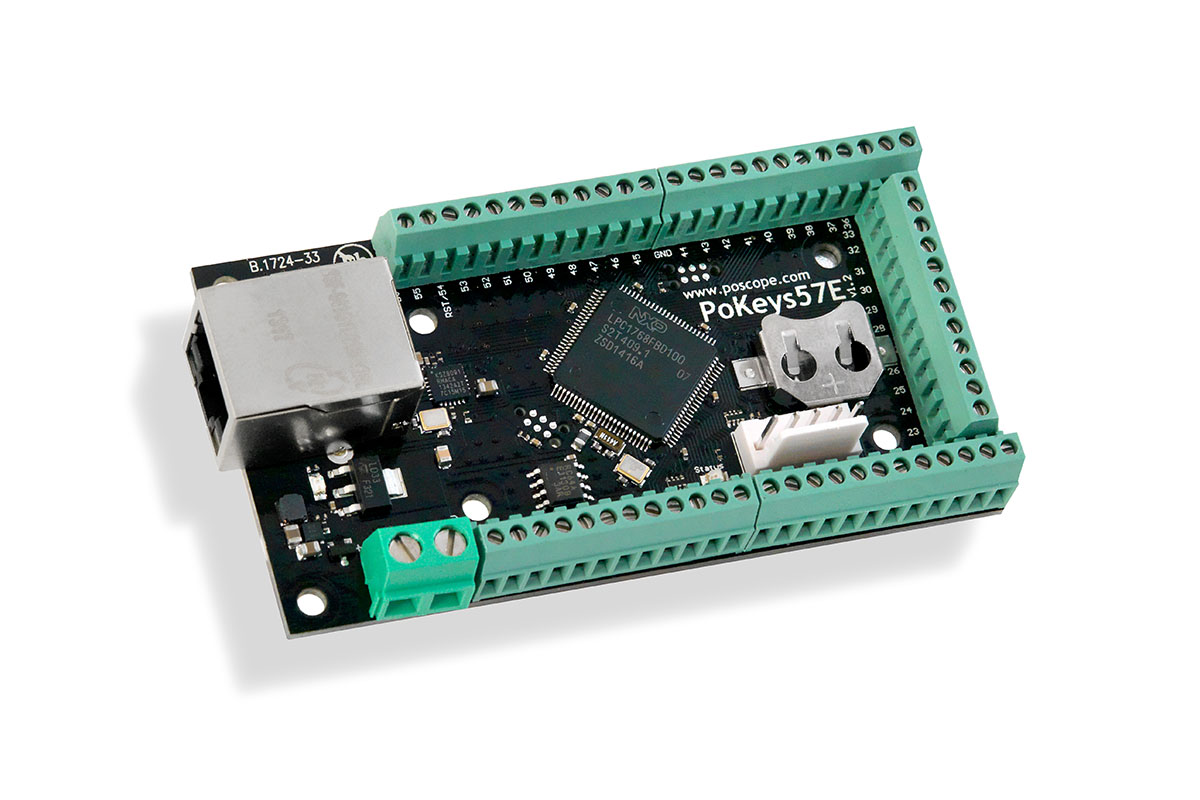
One particularly popular use case is in flight and racing simulators. Enthusiasts often use the PoKeys57E to connect physical buttons, rotary encoders, and LED indicators to simulation software like X-Plane or Microsoft Flight Simulator. Because the device can emulate keyboard inputs, it seamlessly integrates with games and professional training simulators without requiring complex programming.
Programming and Customization
Configuring the PoKeys57E is straightforward thanks to its dedicated PoKeys configuration software, which provides a graphical interface for pin assignment, PWM settings, and encoder configurations. For advanced users, the device also supports custom scripting in Lua, enabling complex logic and automation sequences.
For example, a user could program the PoKeys57E to:
- Read an analog temperature sensor and trigger a cooling fan when thresholds are exceeded.
- Convert rotary encoder movements into virtual joystick inputs for simulator controls.
- Log input states over time for debugging or data analysis.
Why the PoKeys57E Stands Out
Compared to generic USB I/O devices, the PoKeys57E offers a unique combination of versatility, ease of use, and affordability. Its ability to function as both an input and output device—while also emulating keyboards and joysticks—makes it a go-to solution for DIY engineers and professionals alike.
Whether you’re automating a workshop, building a simulator cockpit, or developing a custom control panel, the PoKeys57E provides the reliability and functionality needed to bring your project to life. In the next chapter, we’ll explore another critical tool for enthusiasts and engineers: RC simulator interfaces and their role in remote-controlled vehicle testing.
RC Simulator Interface – Bridging the Gap Between Virtual and Real-World RC Training
For remote control (RC) enthusiasts, pilots, and engineers, RC simulator interfaces serve as a crucial tool for skill development, system testing, and hardware validation. These interfaces allow real RC transmitters to communicate with simulation software, providing an immersive training experience that closely mirrors real-world conditions. By integrating with devices like the PoKeys57E, RC simulator interfaces enable users to refine their piloting techniques, test new configurations, and troubleshoot setups without the risk—or expense—of crashing actual aircraft or vehicles.
How RC Simulator Interfaces Work
An RC simulator interface acts as a bridge between a physical RC transmitter and computer-based simulation programs. Most modern RC transmitters output signals via a trainer port (typically PPM or PWM), USB, or wireless protocols. The RC simulator interface converts these signals into a format that flight or driving simulators can interpret.
Some common types of RC simulator interfaces include:
- USB dongles – Plug-and-play adapters that connect directly to a transmitter’s trainer port.
- Wireless modules – Bluetooth or Wi-Fi-based interfaces for cable-free operation.
- Custom-built solutions – Using microcontrollers (like Arduino) or devices like the PoKeys57E to process and forward signals.
Popular simulation software such as RealFlight, PhoenixRC, and DRL Simulator rely on these interfaces to provide realistic control responsiveness, ensuring that virtual practice translates effectively to real-world piloting.
Benefits of Using an RC Simulator Interface
Risk-Free Training – New pilots can practice maneuvers, recover from stalls, and learn orientation without the fear of damaging expensive RC models.
Hardware Testing – Engineers can validate transmitter configurations, gimbal sensitivity, and failsafe mechanisms before deploying them in actual drones or aircraft.
Weather-Independent Practice – Unlike outdoor flying, simulators allow training in any conditions—rain, wind, or darkness—without limitations.
Cost Savings – Avoiding crashes during the learning phase reduces repair and replacement costs significantly.
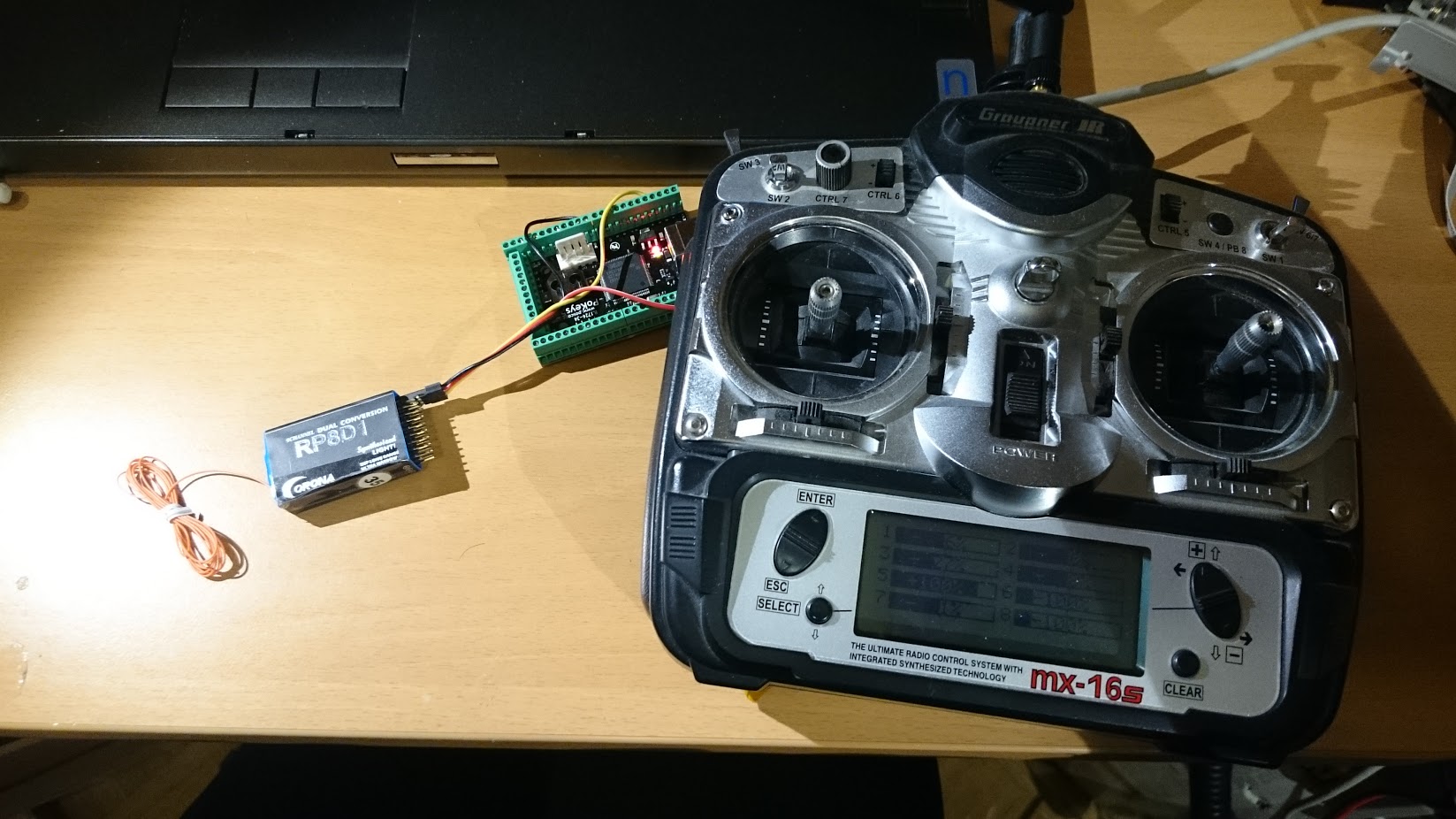
Integration with the PoKeys57E
For advanced users, the PoKeys57E can enhance RC simulator interfaces by adding custom controls and feedback mechanisms. For example:
- Connecting physical switches and buttons to simulate landing gear or camera controls.
- Using analog inputs to replicate additional sliders or knobs not present on standard transmitters.
- Integrating LED indicators to show battery status or flight mode changes within the simulator.
This flexibility makes the PoKeys57E a valuable addition to any RC simulator interface setup, particularly for those building custom simulator rigs.
Choosing the Right RC Simulator Interface
When selecting an RC simulator interface, consider:
- Compatibility – Does it work with your transmitter and preferred simulation software?
- Latency – Low signal delay is critical for realistic responsiveness.
- Expandability – Can additional controls or feedback systems be integrated?
For hobbyists, a basic USB dongle may suffice, while professionals might opt for programmable solutions like the PoKeys57E for greater customization.
RC simulator interfaces are indispensable for both beginners and seasoned RC pilots, offering a safe, cost-effective way to build skills and test configurations. When combined with versatile hardware like the PoKeys57E, they unlock even greater potential for customization and realism.
In the next chapter, we’ll shift focus to another essential tool for engineers and researchers: the Raspberry Pi temperature logger, a compact yet powerful solution for environmental monitoring.
Raspberry Pi Temperature Logger – Affordable and Customizable Environmental Monitoring
Monitoring temperature and other environmental factors is critical across industries—from industrial automation to agricultural management and laboratory research. A Raspberry Pi temperature logger provides a low-cost, highly customizable solution for capturing and analyzing temperature data over time. By leveraging the Raspberry Pi’s GPIO pins and vast ecosystem of sensors, users can build sophisticated logging systems tailored to their exact needs—whether tracking server room conditions, optimizing greenhouse climates, or conducting scientific experiments.
Why Use a Raspberry Pi for Temperature Logging?
The Raspberry Pi temperature logger stands out for several reasons:
Cost-Effectiveness – Compared to commercial data loggers, a Raspberry Pi-based system is significantly cheaper while offering comparable (or greater) flexibility.
Customizability – Users can select from a wide variety of sensors (DS18B20, DHT22, BME280) and program sampling rates, alarms, and data storage formats.
Remote Access & Networking – The Pi’s built-in Wi-Fi/Ethernet allows real-time monitoring via dashboards or alerts through email/Telegram.
Expandability – Additional sensors (humidity, pressure, CO₂) can be integrated alongside temperature logging.
Building a Basic Raspberry Pi Temperature Logger
A simple Raspberry Pi temperature logger requires just a few components:
- Raspberry Pi (any model with GPIO pins)
- Temperature sensor (e.g., DS18B20 digital sensor)
- Breadboard/jumper wires (for prototyping)
- Power supply (micro-USB or USB-C, depending on Pi model)
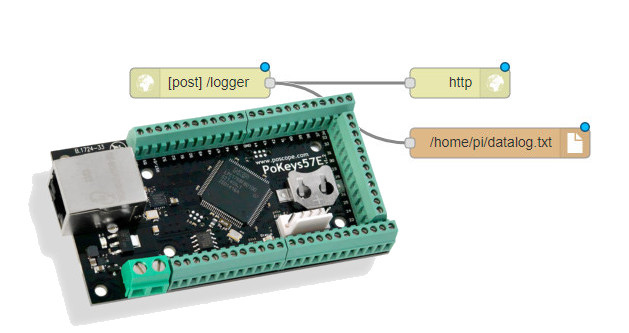
Step-by-Step Setup
Connect the Sensor – Wire the DS18B20 to the Pi’s 3.3V, ground, and a GPIO pin (with a 4.7kΩ pull-up resistor).
Enable 1-Wire Interface – In raspi-config
, activate the 1-Wire protocol for the sensor.
Read Sensor Data – Use Python to read the sensor’s output from /sys/bus/w1/devices/
.
Log Data – Store readings in a CSV file or database (SQLite, InfluxDB) with timestamps.
Visualize Data – Use Grafana, Matplotlib, or a simple web dashboard to display trends.
For more advanced setups, multiple sensors can be deployed across different locations, with the Pi aggregating data via I2C or SPI buses.
Advanced Applications
Beyond basic logging, a Raspberry Pi temperature logger can be enhanced with:
- Cloud Integration – Upload data to AWS IoT, Google Sheets, or Home Assistant for remote access.
- Automated Alerts – Trigger email/SMS notifications if temperatures exceed thresholds.
- Energy Efficiency – Pair with relays to control fans, heaters, or HVAC systems automatically.
Comparing Raspberry Pi to Dedicated DAQ Devices
While DAQ devices (Data Acquisition Systems) offer high precision and industrial robustness, a Raspberry Pi temperature logger is ideal for:
- Budget-conscious projects (a full Pi setup can cost under $50).
- Prototyping and experimentation (easy to reprogram and modify).
- Distributed monitoring (multiple Pis can network over MQTT or LoRa).
However, for mission-critical industrial applications where reliability is paramount, DAQ devices may still be preferable.
The Raspberry Pi temperature logger demonstrates how accessible and adaptable single-board computers have become for environmental monitoring. Whether for hobbyists, researchers, or small-scale industrial use, it provides a perfect balance of affordability and functionality.
In the next chapter, we’ll explore DAQ devices—high-precision instruments designed for professional data acquisition in demanding environments.
From Theory to Practice: Optimizing Stepper Motors with Drivers, Current & PCB Validation
DAQ Devices – Precision Data Acquisition for Industrial and Scientific Applications
While the Raspberry Pi temperature logger offers an excellent entry point for basic monitoring, professional environments often demand more robust solutions. This is where DAQ devices (Data Acquisition Systems) excel, providing high-accuracy, multi-channel measurement capabilities for critical industrial processes, laboratory research, and automated test systems. Unlike consumer-grade alternatives, DAQ devices deliver industrial reliability, precision timing, and specialized signal conditioning to handle complex measurement scenarios.
What Makes DAQ Devices Essential?
DAQ devices serve as the backbone of modern measurement systems, offering several key advantages:
High-Speed, High-Resolution Sampling – Professional DAQ devices support sampling rates up to MHz ranges with 16-24 bit ADC resolution, far exceeding basic microcontroller-based loggers.
Signal Conditioning – Built-in isolation, amplification, and filtering ensure clean measurements even in electrically noisy environments.
Multi-Channel Expansion – Systems can scale from 8 to hundreds of synchronized channels for large-scale monitoring.
Deterministic Operation – Real-time processing and hardware-timed operations guarantee precise timing for control applications.
Leading manufacturers like National Instruments (NI), Keysight, and Advantech offer DAQ devices ranging from compact USB modules to rack-mounted PCIe systems, catering to diverse industry needs.

Common Applications of DAQ Devices
Industrial Condition Monitoring
- Vibration analysis on rotating machinery
- Power quality monitoring in electrical grids
- Temperature/pressure profiling in manufacturing processes
Automotive & Aerospace Testing
- Engine performance characterization
- Structural stress testing under dynamic loads
- In-vehicle network (CAN bus) data logging
Scientific Research
- Neurophysiology experiments (EMG/EEG signal acquisition)
- Material testing in environmental chambers
- Particle detector readouts in physics experiments
Unlike the Raspberry Pi temperature logger, which typically handles slow-changing signals, DAQ devices can capture transient events like voltage spikes or mechanical shocks with microsecond precision.
Key Selection Criteria for DAQ Devices
When specifying a DAQ device, engineers must consider:
Parameter | Typical Requirements |
---|---|
Sampling Rate | 10 kS/s to 10 MS/s depending on signal bandwidth |
Resolution | 12-bit (general purpose) to 24-bit (strain gauges, thermocouples) |
Input Types | Voltage (±10V), current (4-20mA), digital I/O, counters |
Isolation | 250V to 1000V for industrial environments |
Interface | USB, Ethernet, PCIe, or PXI for modular systems |
Advanced features like simultaneous sampling (for phase-accurate measurements) and built-in DSP functionality further distinguish professional-grade DAQ devices from hobbyist solutions.
Integration with Control Systems
Modern DAQ devices don’t just collect data—they actively participate in control loops. When combined with:
- PLC systems for industrial automation
- PoKeys57E for custom I/O expansion
- SCADA software for visualization
they form complete monitoring and control ecosystems. For example, a DAQ device might acquire temperature data from 50 thermocouples in a chemical reactor, then interface with a PLC to adjust cooling valves in real-time.
The Future of DAQ Technology
Emerging trends in DAQ devices include:
- AI-accelerated edge processing (running machine learning models directly on DAQ hardware)
- Wireless sensor networks (5G-enabled distributed measurements)
- Quantum computing interfaces (ultra-low-noise readout electronics)
While the Raspberry Pi temperature logger remains ideal for educational and light-duty applications, DAQ devices continue pushing boundaries in measurement science—enabling breakthroughs from nanotechnology labs to smart factories.
DAQ devices represent the gold standard for precision measurements, bridging the gap between physical phenomena and digital analysis. Their unparalleled accuracy and reliability make them indispensable for engineers and scientists working on cutting-edge technologies. In our final chapter, we’ll synthesize how PoKeys57E, RC simulator interfaces, Raspberry Pi temperature loggers, and DAQ devices can interoperate in comprehensive monitoring and control systems.
Integrating PoKeys57E, RC Simulator Interfaces, Raspberry Pi Temperature Loggers, and DAQ Devices for Comprehensive Control and Monitoring
The technological landscape offers a spectrum of hardware solutions, each excelling in specific applications—from hobbyist projects to industrial automation. Throughout this article, we’ve explored four powerful tools: the versatile PoKeys57E, immersive RC simulator interfaces, cost-effective Raspberry Pi temperature loggers, and precision DAQ devices. While each serves distinct purposes, their true potential emerges when integrated into cohesive systems that leverage their complementary strengths.
Synergistic Applications Across Domains
Custom Simulation Rigs
The PoKeys57E forms the ideal backbone for simulator setups, managing physical controls (buttons, encoders, LEDs) while the RC simulator interface translates transmitter inputs into virtual commands. Adding a Raspberry Pi temperature logger could monitor hardware thermals, preventing overheating during extended sessions, while a compact DAQ device might capture force feedback signals for advanced haptic systems.
Smart Industrial Workstations
In prototyping labs, DAQ devices handle high-speed sensor measurements, with the PoKeys57E providing supplementary I/O for operator controls. A network of Raspberry Pi temperature loggers could track environmental conditions across facilities, feeding data into the central DAQ system for comprehensive analytics.
Research & Development Platforms
Scientific experiments often require hybrid solutions—a DAQ device for precision analog measurements, augmented by the PoKeys57E’s digital control capabilities. Meanwhile, Raspberry Pi loggers offer distributed monitoring at lower cost points, and RC simulator interfaces might even find use in robotics research for remote control prototyping.
The Future of Integrated Hardware Systems
Emerging trends point toward even tighter integration:
- Edge computing combining Raspberry Pi processing with DAQ device precision
- IoT convergence allowing PoKeys57E controls to interact with cloud-based DAQ analytics
- AI-enhanced simulation where RC interfaces feed real-world data into adaptive training algorithms
Reimagining Railroads: The Role of USB I/O Controllers in Streamlining Model Railway Systems
Final Thoughts
Whether you’re an engineer designing complex automation systems, a researcher collecting precise measurements, or a hobbyist building immersive simulators, today’s hardware ecosystem offers tailored solutions at every level. The PoKeys57E provides unmatched flexibility for control applications, RC simulator interfaces bridge physical and virtual worlds, Raspberry Pi temperature loggers democratize environmental monitoring, and DAQ devices deliver laboratory-grade precision. By understanding their capabilities and interoperability, you can architect systems that are greater than the sum of their parts—pushing the boundaries of what’s possible in automation, simulation, and data acquisition.